Discussing building energy management can be overwhelming. Everyone wants to save energy and money, but utility contract negotiations, retrofitting HVAC systems, renewable energy, and battery storage can add a lot of complexity to the conversation. With numerous retro-commissioning projects under our belt, we want to share our knowledge with building owners and facility managers so you can be better equipped to have these discussions and find relatively easy energy savings opportunities in your facilities. Over the next two months, we will be sharing several low and no-cost energy conservation measures (ECMs) that can help you save operating dollars without sacrificing occupant comfort.
The Easiest Energy to Save is Energy You Don’t Use
Growing up, I’ll always remember the yell from my father as we were leaving the house: “make sure all the lights are off!” I would scramble around the house, turning all the lights off that I, of course, accidentally left on. For a house, turning things off is the simplest way to save energy! From the lights to the thermostat, shutting things off has and always will be the best way to lower your utility bills. Scaling up to commercial-sized buildings, the same method applies.
When a new building is constructed and commissioned, the equipment operating schedules are often fine-tuned and limited to the true hours of operation. However, after years of operation, these schedules tend to widen, and the hours of operation begin to rise. There are many reasons for schedules to increase or drift: change in use of the building, seasonal temperature complaints during certain times of the day, or that one Saturday event where the HVAC was scheduled on and never removed after. Unfortunately, these small changes result in a substantial increase in energy consumption. For each hour of scheduled operation, an air handling unit must operate continuously. During this time, outside air must be heated and cooled as required for ventilation, while simultaneously maintaining space temperature at occupied comfort levels.
Now let’s look at the math. Let’s assume a building has five air handling units and each unit is equipped with a 20 HP (14 kW) constant volume supply fan. Due to drift in the building schedule, the fan operates seven days a week from 5:00 a.m. to 10:00 p.m. or 6,205 hours per year. After reviewing with the building staff, it is determined that the schedule can be shortened to 7:00 a.m. to 10:00 p.m. Monday through Friday, or 3,900 hours per year. Assuming the electrical rate is billed at $0.13/kWh and a reduced runtime of 2,305 hours, a simple schedule change for this building would result in approximately $21,000 per year in fan energy savings! Note, this calculation does not consider the additional energy savings associated with no longer heating or cooling the outside airflow (which can typically exceed the dollar savings of fan energy savings).
Before adjusting schedules, it is beneficial to meet with building occupants. They know when and how the building is used. This meeting will ensure that the schedules are accurate to the building’s occupancy and will help avoid future complaints from occupants. It is also important to recommission the unoccupied mode and morning warm-up controls to ensure they work properly. An occupancy schedule may be extended because the building is not warm enough or cool enough by the time the occupants arrive. By ensuring the unoccupied controls operate properly and setpoints fit the current facility needs, savings can be maximized without affecting human comfort. Lastly, staff should always be trained on the proper way to use the scheduling system and the costly effects of improperly scheduling equipment. Making sure the building automation system’s occupancy schedule matches the building’s true occupancy, the unoccupied controls operate properly, and providing sufficient training is the best way to ensure persistent energy savings are achieved.
Take a look at our other ECM tips here. If you have any questions about this article or think you might be able to apply this strategy in your facility and would like to learn more, please contact us here.
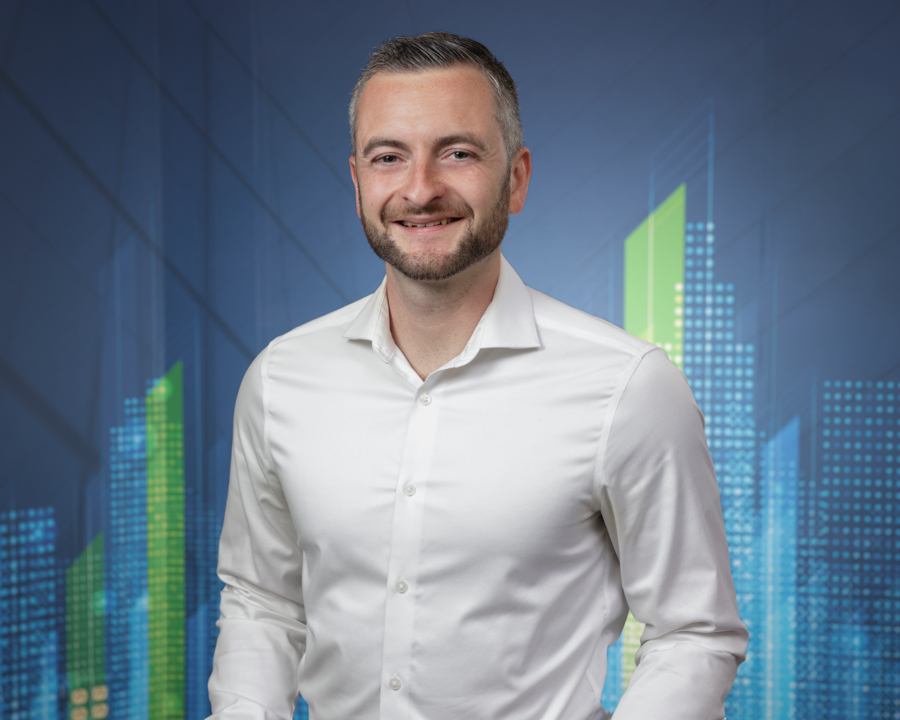
About the Author:
Brian Messerschmidt is a Project Manager at Sustainable Engineering Solutions. He has managed numerous Commissioning and Retro-Commissioning projects throughout Connecticut and Massachusetts. Brian earned his B.S. in Mechanical Engineering from Central Connecticut State University. He is a registered Professional Engineer in the State of Connecticut and a Certified Energy Manager.