As a facility manager, you’re likely always looking for ways to improve your building’s performance and reduce energy consumption. One of the ways you can accomplish this is to implement a retro-commissioning program within your facility. Retro-commissioning, or RCx, involves identifying and fixing problems in an existing building’s systems to optimize performance and reduce energy waste and energy costs (check out our “What is Retro-Commissioning?” article for a more in-depth explanation of the RCx process and its benefits). You may think you have neither the time nor the budget to undertake a thorough retro-commissioning process. If your utility company offers retro-commissioning incentives, you may be eligible for technical and financial support. However, there are immediate steps that you and your staff could easily implement to get you on your way to improving your facility’s performance.
Here are five simple things you can do to reduce HVAC energy consumption and improve your building’s performance through retro-commissioning. These five items are based on some of the more common issues we have found over the years when performing RCx studies in facilities.
1. Review and Adjust Your Building Automation System schedules for equipment.
Your building automation system (BAS) is the brain of your building’s HVAC system, controlling everything from temperature and ventilation to equipment operating schedules. The operating schedules for various pieces of equipment often do not accurately reflect the occupancy schedules for a building period. This is especially common in facilities that frequently change occupancy schedules for portions of a building, such as educational facilities or places of assembly. We commonly find equipment operating schedules set up to run much earlier and later than when a building or space will be occupied. Adjusting the operating schedule to match the actual occupancy schedule can eliminate several hours of operation, thus reducing energy usage and operating costs. Take the time to review and adjust your operating schedules to ensure they’re optimized for your building’s usage patterns.
2. Clean and Maintain Your HVAC Systems.
Over time, dust, debris, and other contaminants can accumulate in air handling systems, specifically on filters in front of heating and cooling coils. If filters are not changed regularly, they can become clogged, leading to greater air resistance (higher pressure drop) and increased fan energy usage. In extreme situations, unmaintained filters can even collapse due to increased pressure and deterioration, allowing dust and debris to contaminate heating and cooling coils, airflow measuring devices, and other sensors, resulting in poor heat transfer and inaccurate sensing of airflow and air temperature. All of this leads to significantly diminished system performance. Regular filter changes, along with cleaning and maintenance, can help ensure your system is running at peak efficiency.
3. Examine outside air dampers on air handling systems for dampers that are stuck or not responding properly.
As air handling systems age, various components and devices wear, become loose, and deteriorate. This is particularly noticeable with mechanical components that cycle back and forth, such as outside air dampers. It is common to find damper actuators, linkages, and damper blades operating with excessive play or stuck in certain positions. When this happens, outside air dampers can allow excess outside air to be brought into air handling systems, which results in increased energy usage to heat and cool the excess air. Examining the operation of outside air dampers and associated mechanical linkages and actuators for appropriate movement and repeatability on a regular basis will minimize excess outside air and prevent this increased energy usage.
4. Look closely at pumps operating with VFDs.
Variable frequency drives are commonly used on hot water and chilled water pumps to modulate speed and, thus, flow to the various HVAC systems in a building. VFDs are great energy-saving devices that allow pumps to change speed and adapt to the system pressures required to deliver flow. However, it is also quite common for triple-duty valves to be installed on the discharge of pumps. Traditionally, triple-duty valves were used as isolation and balancing valves on pumps. They are commonly left in pumping systems when VFD retrofits are installed. However, we commonly find that these balancing valves are still left in a throttled position from the original construction. This creates added resistance (false head) in the pumping system that is no longer necessary because VFDs have been installed. These balancing valves should be fully opened to allow the VFDs to modulate the pumps to their lowest speeds possible and to provide the greatest energy savings.
5. Check the building’s air pressure.
If you’ve ever opened a door to a building and felt a blast of air coming out or air being sucked into the building, that’s a sign of a significant air pressure problem in the building. Air pressure issues result from too much or too little outside air being brought in by air handling systems or too much or too little exhaust air leaving the building. The imbalance can result in increased energy costs by conditioning excess outside air (air blowing out of the building) or space comfort problems resulting from uncontrolled infiltration (air being sucked into a building) caused by high exhaust rates. Excess outside air could be the result of the issue discussed in item #3 above and can be easily remedied. If the outside air dampers are stuck closed and not allowing sufficient make-up air for exhaust systems in the building, they may also cause air to be sucked into the building. This could also be caused by exhaust fans operating at a higher air flow rate than designed. The root cause of either scenario can be quickly identified by understanding what systems are operating and if they are operating in the correct modes.
These are some of the simpler issues that we have found through retro-commissioning efforts for various buildings, and they can be readily identified and diagnosed by a facility manager. These are typically no-cost or low-cost fixes that can be implemented by in-house staff that reap notable savings and operating improvements. By checking these five simple items, you can optimize your building’s HVAC system, reduce energy waste, and create a more comfortable and sustainable environment for your building’s occupants.
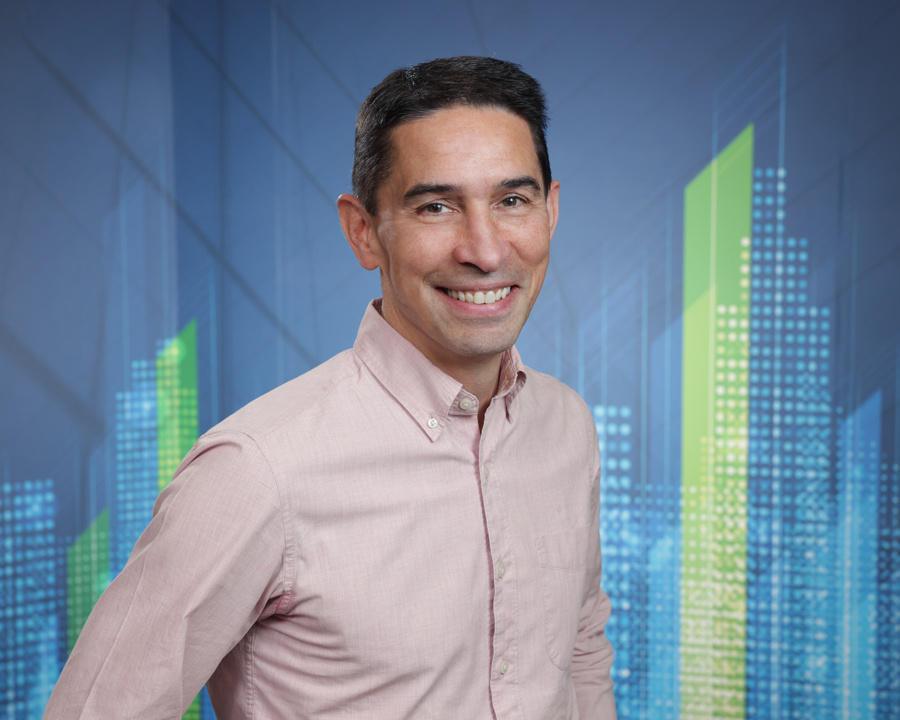
About the Author:
Ernest Lawas is the co-founder and a Managing Principal at Sustainable Engineering Solutions. He has over 25 years of experience providing Commissioning services nationwide. Ernie is a registered Professional Engineer (P.E.) in Connecticut, New York, New Jersey, and Massachusetts. He is also a Certified Commissioning Professional through the Building Commissioning Association, a Certified Energy Manager and Certified Energy Auditor through AEE, and a LEED Accredited Professional.