In our previous article, “What is Retro-Commissioning?”, we covered some of the signs that may indicate that your facility could benefit from Retro-Commissioning (RCx). In this article, we’ll dive deeper into some of those signs, discussing what they mean and what problems they may be symptomatic of.
Increased energy consumption
It is not the cost of your energy usage, but rather the consumption of that energy itself, that indicates that RCx may be needed. Higher energy costs alone may simply be explained by an increase in the unit cost of energy. However, higher costs may also result from an increase in total energy usage or higher peak demand of electricity.
Let’s look at a simple example of how an electric rate structure impacts energy cost and what that means. Most commercial and institutional electric utility customers have a rate structure that charges based on two components: the total energy used in kilowatt hours, or kWh (consumption), and the greatest peak demand in kilowatts, or kW, over the billing period. Overall electric utility costs can go up because of
- an increase in the cost of electricity ($ per kWh),
- an increase in the utility consumption and
- an increase in peak demand power.
In the last case, the consumption values would be the same but the total utility cost is higher because the demand is higher. So, for cases b and c above, tracking utility consumption, demand and cost are important to determine if there is an issue that needs investigated or if increase in utility costs are only a function of rising energy costs.
Energy consumption can also change seasonally depending on the type of utility used by your heating and cooling equipment. For example: if building cooling during the summer months is provided by electrically powered air conditioning equipment and wintertime heating equipment uses natural gas, the summertime electric energy consumption will be higher than winter, and vice versa for natural gas consumption. Looking at this energy consumption year over year and seasonally is key to recognizing a larger trend of increased energy usage over time. When looking at seasonal energy and demand usage it is important to know if one season was hotter or colder than the previous one to identify legitimate trends in the increase in energy consumption. This can be done by examining if one cooling or heating season was hotter or colder than the previous and adjusting the comparison accordingly to make sure the comparison is apples to apples.
Occupant comfort complaints
Occupant comfort complaints can stem from numerous issues. With HVAC systems, they typically result from one of two root causes: a heat transfer problem or a building automation controls (BAS) problem.
Heat Transfer
In the case of a heat transfer problem, let’s say occupants are complaining of cold areas in the building from one heating season to the next. The building operators notice that the areas are not making the heating setpoint as required. Additionally, the operators have noticed the heating hot water pumps serving the air handlers are running at higher speeds than before, and there is an increase in natural gas usage and utility costs.
In this example, we’ll start by looking at the utility consumption data and comparing seasonal energy usage. The data indicates that the recent heating season was not as cold as the previous, and therefore not the cause of the increase in energy usage. However, by performing a physical inspection of the air handling units we discover that numerous heating hot water coils are dirty, preventing the proper heat transfer from the heating hot water to the airstream. This resulted in cold complaints and higher energy usage. By cleaning the coils, proper heat transfer is restored, the complaints are resolved, and natural gas consumption is reduced to normal seasonal usage.
Building Automation Controls
Now let’s look at a simplified building automation controls problem. We’ll use the same scenario in which occupants have started complaining of cold areas or zones of a building. The building operators notice that the spaces are cold from space thermostat readings, however the air handling units serving those spaces appear to be operating correctly with the proper supply air temperature being delivered to the spaces.
By performing a control system point to point verification for the air handling units during an RCx study, we identify that the discharge air temperature sensors on the units are out of calibration by several degrees. This resulted in air being supplied by the units at a lower temperature than what was read by the BAS, which was the root cause of the cold areas. By recalibrating or replacing these sensors, the complaints should be resolved.
In this next example, let’s breakdown occupant complaints of stuffiness in a space. Complaints of space stuffiness have increased over time. Additionally, the occupants have started complaining about drafts and have indicated that the doors to the building are harder to open. The building operators cannot identify any deficiency with the air handling unit serving the space, and all of the parameters monitored by the BAS indicate that the air handling unit is operating normally.
By performing a thorough review of the control system for the air handling units during an RCx study, we identify that the outside air dampers on the air handling unit have broken and are not bringing in sufficient ventilation air. Proper amounts of ventilation air are required for occupant health, preventing the feeling of stuffiness, and maintaining a neutral or slightly positive building pressure. By repairing the outside air damper, the stuffiness and draft feelings are eliminated and the entrance doors to the building open normally.
These are just a few common examples of issues that can be solved with RCx, though every building is unique and can have varying root causes for the same issues. The change of seasons is a great time to prepare for the next heating or cooling season and evaluate the performance of your facility’s systems. If you’re experiencing any of the issued described above or in our previous article, now may be a good time to have your facility retro-commissioned!
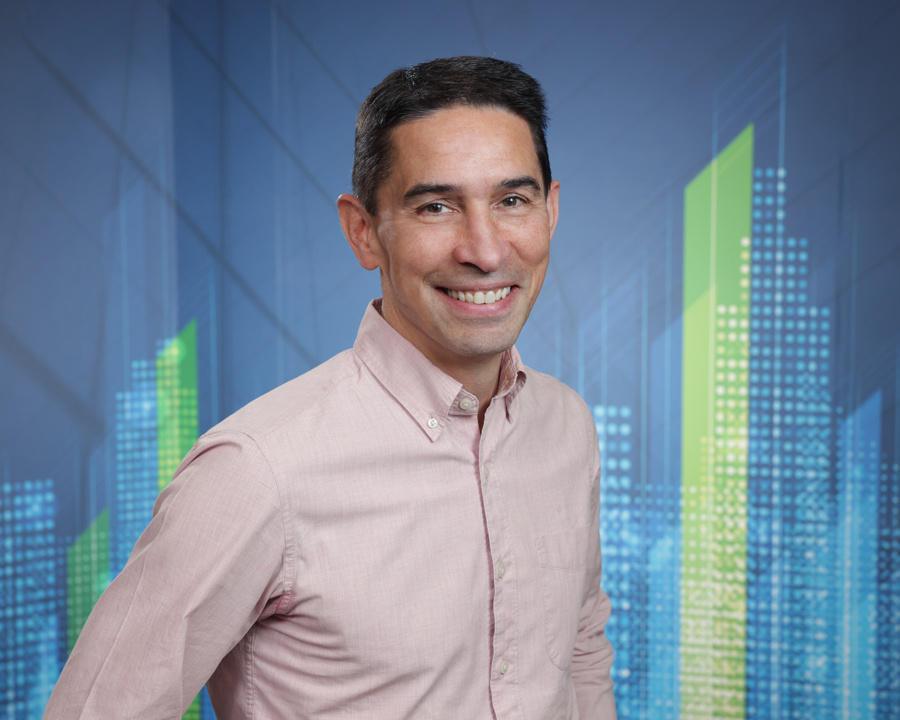
About the Author:
Ernest Lawas is the co-founder and a Managing Principal at Sustainable Engineering Solutions. He has over 25 years of experience providing Commissioning services nationwide. Ernie is a registered Professional Engineer (P.E.) in Connecticut, New York, New Jersey, and Massachusetts. He is also a Certified Commissioning Professional through the Building Commissioning Association, a Certified Energy Manager and Certified Energy Auditor through AEE, and a LEED Accredited Professional.