Since the onset of the COVID-19 pandemic in 2020, the construction industry has faced unprecedented challenges in the supply and distribution of equipment and materials. Costs soared, lead times increased, and delays became commonplace—especially for electrical equipment. Among the most significant delays was the availability of main switchgear, which is essential for establishing permanent power in a building. Even in years later, the industry continues to grapple with these effects, leading to scenarios where buildings appear complete but remain inoperable, awaiting permanent power.
However, securing permanent power is only the beginning. Many project teams underestimate the time required to turn over a building once permanent power is established. This milestone is critical for initiating essential activities such as equipment startups, HVAC controls integration, testing, adjusting and balancing (TAB), and commissioning.
Equipment Startups
The startup of mechanical and electrical equipment is one of the first activities that depend on permanent power. Equipment startups are crucial as they ensure the manufacturer’s installation requirements are met and verify that the equipment is safe and operational. Clean startups not only signal readiness for subsequent activities but are also often tied to equipment warranties. Any issues during startups could result in warranty voidance or costly rework, making this phase a high-stakes milestone.
HVAC Controls
HVAC control systems rely on permanent power to perform initial checkouts and begin point-to-point testing. While controllers and wiring can be installed beforehand, the equipment cannot function until it receives stable, permanent power. Additionally, IT infrastructure, such as network connections, must be operational to test communications between controllers and building automation systems (BAS). Without permanent power, the progress of HVAC controls remains at a standstill, delaying system optimization and coordination.
Testing, Adjusting, and Balancing (TAB)
The TAB process typically follows the completion of equipment startups and controls integration. TAB contractors rely on fully operational systems to measure and adjust airflow, water flow, and other parameters. A completed controls system is essential to manipulate valves, dampers, and other components during the TAB process. If control systems are not properly vetted before TAB begins, the risk of delays and rework increases significantly.
Commissioning: Final Functional Testing
The commissioning phase is the culmination of all prior activities. Functional testing, performed by the commissioning agent, ensures that all building systems operate as intended. For commissioning to proceed smoothly, equipment startups, controls integration, and TAB must be first completed and verified. By establishing a clear sequence of activities tied to permanent power, the project team can minimize deficiencies and ensure a more efficient commissioning process.
Mitigating Delays and Preparing for Permanent Power
Given the persistent delays in securing permanent power, project teams must adopt proactive strategies to prepare for a quick turnover once power becomes available. Key steps include:
- Commissioning Team Coordination: Organize meetings to align on equipment startups, controls integration, and TAB work. This is an opportunity to address potential issues, such as packaged controller integration, automated temperature control (ATC) sequences, TAB setpoints, and the review of TAB plans.
- Physical Inspections: While awaiting permanent power, the team can conduct final walkthroughs to verify field installations, such as piping, insulation, labeling, and nameplates. Addressing these items in advance reduces delays once systems are powered.
- Turnover Document Preparation: Begin gathering turnover documents, including operation and maintenance (O&M) manuals and training agendas. This can help ensure the O&M manual is ready during turnover and training sessions are already outlined and ready to be scheduled.
Permanent power is a pivotal milestone in building projects, directly influencing the schedule and quality of downstream activities. Equipment startups, controls integration, TAB, and commissioning all depend on its timely establishment. Without permanent power, project teams face significant delays, increased costs, and potential operational issues.
By understanding the importance of permanent power and preparing for its availability, project teams can mitigate risks, streamline turnover, and deliver a building that performs reliably from day one. While construction schedules will always be tight, the adage “a building is only built once” serves as a reminder to prioritize quality and coordination for long-term success.
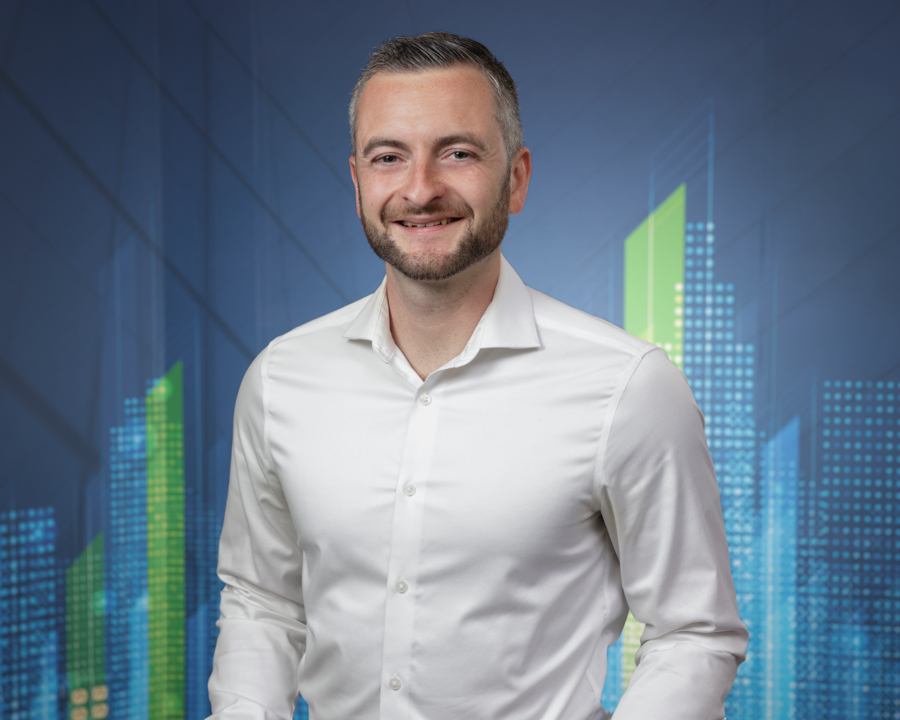
About the Author:
Brian Messerschmidt is a Project Manager at Sustainable Engineering Solutions. He has managed numerous Commissioning and Retro-Commissioning projects throughout Connecticut and Massachusetts. Brian earned his B.S. in Mechanical Engineering from Central Connecticut State University. He is a registered Professional Engineer in the State of Connecticut and a Certified Energy Manager.